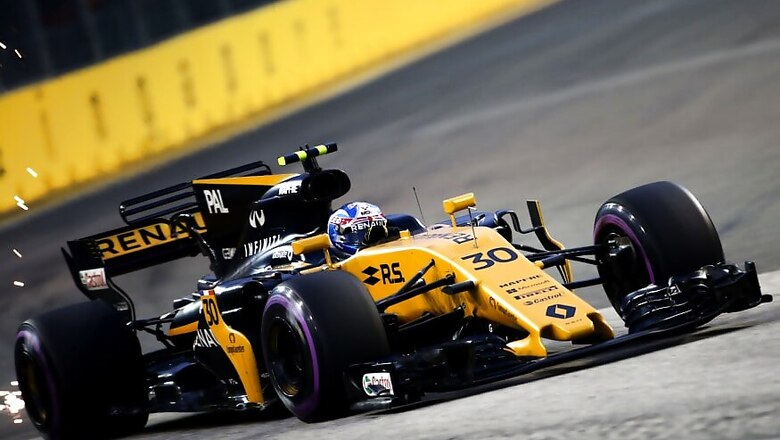
views
From the old-school way of shipping physical servers for all races to almost developing parts in its factories real-time during an on-going race, it has been quite a digital transformation for the present day Renault Sport Formula One Team.
Formerly known as Lotus F1 team, back in 2012, the team had partnered with Microsoft to fine-tune its operations. Of course, the story was all about more speed. But more importantly for Renault, being a highly agile business was another prime focus when they had partnered with Microsoft.
The then Lotus F1 team had opted for Microsoft Dynamics AX ERP solution in 2012 to start the long standing collaboration with Microsoft to basically help in managing the design of a race car. In 2014, the partnership was renewed and the F1 team gained access to Microsoft’s R&D team in Redmond to customise software as they required. Not to forget, the F1 team had received substantially smaller budget when compared to top F1 teams and also radical F1 rule changes forced them to innovate quickly.
A year later, the Renault Sport team deployed Microsoft Cloud including Dynamics AX and Office 365. By 2016, the Renault F1 team had successfully placed itself on cloud. This enabled seamless integration between Dynamics AX and Power BI with Office 365 for Business.
For those unaware, the Renault team used to ship its physical servers to every location for the 21 races it competes just to ensure they had the performance they needed. Microsoft Cloud relieved them of this hassle. Also, with the cloud-based Dynamics AX, the team could have remote access to data for its off-site facility to develop parts real-time.
Renault Sport CIO Pierre d'Imbleval in an interaction with Debashis Sarkar of News18.com, at the recently held Singapore Grand Prix, shares why Renault Sport Formula One Team opted for Microsoft solutions like Dynamics AX, Office 365 and Azure in its race to the podium.
How big is Formula One as a sporting event?
There is a cumulative audience of 1.6 billion people watching Formula One races across the globe annually. With over 425 million unique TV viewers providing 31,000 hours of coverage every year across 200 broadcast countries and 119 broadcasting networks, Formula One is one the most spectacular annual sporting event.
Overview
Renault Sport Formula One Team operates from two main factories-- Whiteways Technology Centre in Oxfordshire, United Kingdom and Hybrid Power Unit Centre in Paris, France. The Whiteways Technology centre caters to design and manufacturing needs of F1 cars. All the brakes, suspension, gear box, chassis and aerodynamics research come from there. On the other hand, the facility in Paris takes care of power requirements of the engine starting right from the complex battery configurations.
Business Challenges
Operational Efficiency: It doesn’t count if you have a fast car if that car is not reliable. Also, gaining efficiency means close coordination among the two facilities and the race venue.
Use up-to-date technology to deliver performance: The team wanted to maximise data analytics approach by harnessing the power of Big Data, Artificial Intelligence, Machine Learning and cloud computing.
Microsoft solutions deployed:
Dynamics 365, Power BI, Microsoft Azure and Office 365.
Why Dynamics 365 and Power BI?
We are using Dynamics 365 especially for all the manufacturing, controlling and operating environments. We start by sending an engineering change to the manufacturing unit. Once a car part is manufactured, data regarding each part of the car is tracked with Dynamics 365 so that we know precisely what part has been used in which car during what race and session.
Apart from minimising the weight and to maximise the lifespan of a car part, this information is crucial for the safety of the driver as well. With this we have precise date regarding around 20,000 car parts and Dynamics 365 helps us in sharing this information in a very short time during the entire lifecycle. Power BI also helps our team to stick to the budget during a season.
Real-life example:
I was in Barcelona in a pre-session test in March. On a Wednesday, we got to know that a car part was not delivering the expected performance. We informed the factory about this at the end of the day. Then the Aerodynamics team reworked and made some simulation on the supercomputer and then the car part was 3D printed and sent to the race tracks on Friday.
Benefits
Dynamics 365 and Power BI helped in gaining agility, improved efficiency in manufacturing, reduced time to take decisions and also simplified infrastructure.
Why Office 365?
The architecture that was set in place, two years ago, to run the communication system was complex. Office 365 simplified this and also introduced new features. Office 365 reduced on premise storage and backup by more than 1 Tb. It drastically reduced travel and flights (between two main factories) by 50 percent and also reduced the team’s mobile phone costs by 30 percent. Additionally, pre-package tools like Yammer, Microsoft Teams enhanced cross-site communication.
How do you collect data from F1 cars and benefits of using Azure?
When a car is running on tracks, it sends thousands of data series through its on-board telemetry. This is re-computed on the local data centre that is setup at each track. Then the engineers get all those data channels to analyse them on the track itself, real time.
We are not allowed to do much of physical tests with the cars. It is only twice a year. Once in Barcelona before the season and the second time at Hungary during the mid-season. To tackle this difficulty, we have a simulator. But in order to build the simulator and make it replicate real racing scenarios we need this precise data.
The most difficult car part to simulate is the tyres. Those big pieces of rubber behave in a very tricky manner depending on the temperature, aggressiveness of the driver and weather conditions. All of these are hard to precisely simulate. In order to learn how a tyre degrades over time, we push two entire race season of data into the cloud and start to analyse that data to predict some generic behaviour of the tyre and put this into the simulator. This will ultimately make the driver get the real sense of tyre degradation while he is simulating.
We collect data about the mood of the driver during each lap of the race to offer feedback regarding how it is impacting the car (like tyre or engine temperature). This is also fed to the simulator to make the car driver-friendly for the next race. This personalised data on the car setup keeps changing from driver to driver and has utmost importance in the racing world.
Benefits
-Improved knowledge of car setup.
-Improved knowledge of tyres.
-Big boost on compute capacity. The team can run simulations on one server or 100,000 servers depending on urgency.
(Disclaimer: The author attended Singapore Grand Prix at Marina Bay Street Circuit, Singapore on the invite of Microsoft India.)
Comments
0 comment