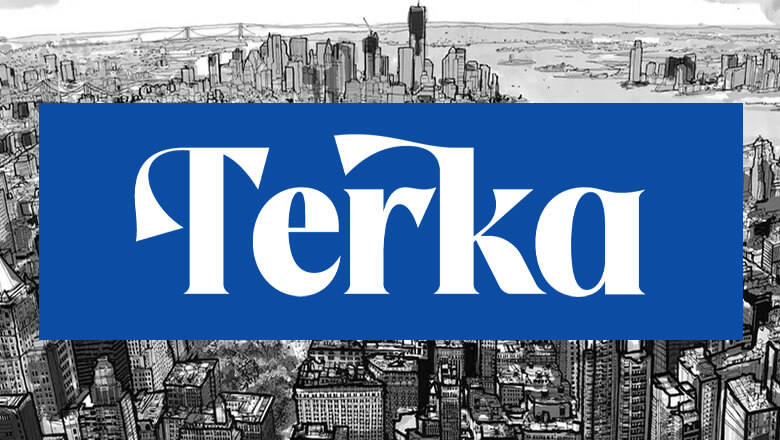
views
THIRUVANANTHAPURAM: You need some time to come to terms with the fact that you are standing at a depth of 4.25 m from the road surface. We were in the trench made at Museum Junction through which pipelines will be laid across the Junction, using the jack and push method, as part of the Japan International Cooperation Agency (JICA)-assisted water supply project for the Kerala Water Authority (KWA). Pipes would be lowered into the trench and laid across the road, without cutting open the road. In fact, the pipes would be pushed inside, thus posing no trouble to vehicular or pedestrian movement. While Electrosteel is the contractor, the labourers are from Elmico Engineering Pvt Ltd. The work is being carried out by 14 labourers, who hail from West Bengal- Haren, Dileep, Lakshman, Bablu, Santhosh, Tapan, Vikas, Sushant, Sunil, Nimay, Dinesh, Dulal, Pradip and Indrajit. Haren, the senior hand, says, “I have been doing similar work for seven years now. It was not easy in the beginning. Now, there is no fear.” They would be working at the site for the next 40 to 45 days, taking one branch to the other side of the road - to the Museum premises - where it would be connected to a pipeline already laid there. Another branch will go to the Observatory, thus covering a total of 60 m. The team has already done similar work at Stationkadavu, Kuzhuvila, Kulathur, Venpalavattom, two spots at Ambalamukku and Killippalam. “This is the toughest, because the soil is very hard here,” says K M John, safety officer with Electrosteel. The open trench is made for the machines and labourers to get down and work. The basement is concreted, at 4 inch thickness, using 8 mm thick iron rods in this case. A rail with four beams is then constructed and fixed using 2- inch-thick concrete. Casing pipes are laid first, inside which the distribution pipeline would be laid. Fifty 1,250 mm-long, 1,200 mm-diameter Mild Steel (MS) pipes of 12 mm thickness will be laid to form the casing pipe, inside which the 1,016-mm MS pipes will be placed. The pipes are pushed using the jack, which has a 70-tonne capacity. “We have four such jacks. In a single push, the pipe can be pushed up to 500 mm,” says Raja Nag, site supervisor with Elmico. R H Ghosh is the other supervisor of Elmico. One casing pipe has been laid now. Initially, it is the natural lighting using a mirror that provides lighting inside the pipe so that a labourer can sit inside and cut through the earth. “As the work progresses, they will be provided with lights, oxygen mask, exhaust fan, safety belts, a trolley for removing the soil and a bell will be tied on their hands so that in case of any emergency they can ring it,” the officials explain. Risks are umpteen. “The soil might collapse. Or, there might be some old trenches in the passage. Lack of air can always be dangerous. In fact, after laying four casing pipes, the labourers always get inside the passage burning a piece of paper so as to ward off foul air. The going has been smooth so far here,” John says.
Comments
0 comment